asked and never gets answered by anyone to my satisfaction. I've been trying to wrap my head around it for a few years whenever I feel the need for a headache and this is where I'm currently at: We all agree there is a centripetal force dependent upon RPM and distance and as you pointed out we should all agree the rod drilling exits at a greater radius than the main journal entrance, which should result in a higher pressure at the rod bearing... but I think it’s what happens in between these two points that is the issue. A picture speaks a thousand words, and in this instance it may be millions, so for reference I made a quick sketch of the different types of crankshaft oiling schemes. Note, the term cross-drilled is heavily over-used and not all “cross-drilled” crankshafts are done in the same manner.
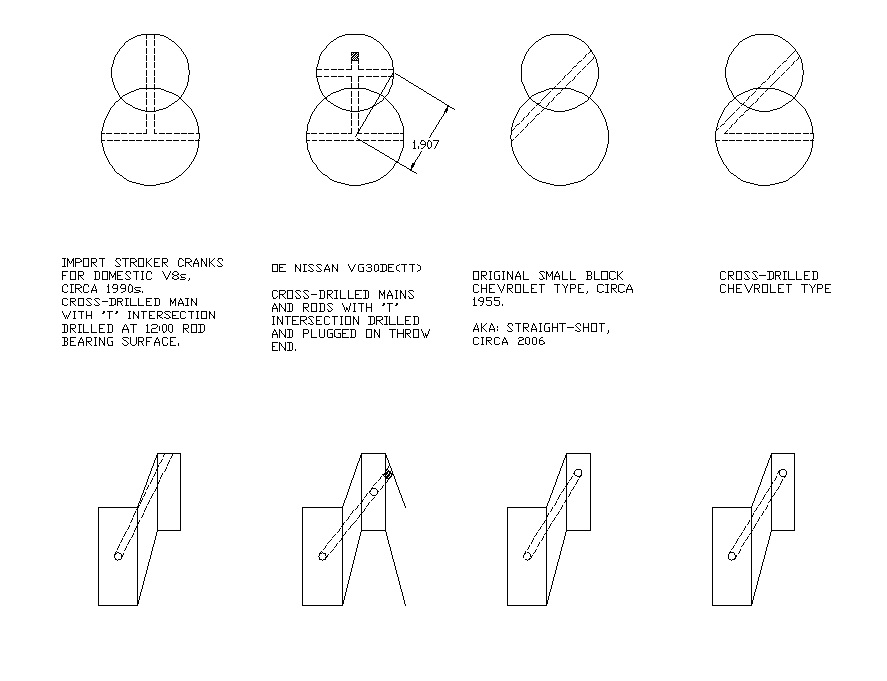 Below is a new graph that shows PSI at various radii, at 8000RPM. If we have 8000RPM then to initiate flow towards the rods, 36psi oil pressure is needed to equal the centripetal force. Since the rod drilling is on a larger radius (AutoCAD tells me it's 1.907", see above), its centripetal force at 8000 RPM is 86psi. 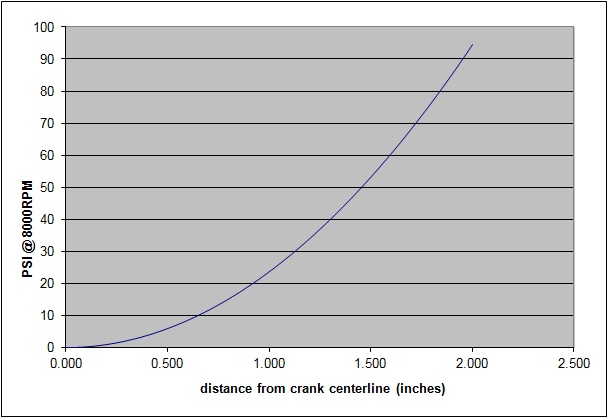
That's a lot of dP. In this instance, I assume zero flow so the pressure at the center of the main cross-drilling is 0PSI, dP of 36PSI at each end, and dP of 86PSI at the end of the rod oil hole(s). We don't just want equilibrium in pressure, we want flow of oil to the rods, and enough to satisfy the leakage past all of the clearances. Is it enough to simply supply the rod journal drilling with an oil reservoir to draw from and the cetripetal force will generate the pressure needed to support the hydryostatic wedge between the journal and bearing?... I'm not sure. But wait, the OE drillings have two 90° corners in the path to take into account which become a restriction as flow increases and can be gauranteed to have a negative effect on dP. In my opinion the OE drilling T intersection in the middle of the main journal at some “X” RPM and oil condition (heat, viscosity, aeration, fuel dilution, etc. etc.) can result in a dP where the oil and/or its impurities can flash to vapor and cause in effect a vapor lock situation that will starve the rod of oil, effectively killing it. I believe the benefits of the straight-shot drilling versus the OE drilling and are two-fold but both relate to dP: 1) straight-shot has no internal 90° angles for the oil to navigate and this reduces the maximum dP within. 2) straight-shot does not cross the center of rotation, so the maximum dP between within is not as high as the OE drilling is exposed to. I've made a statement that plugging the cross-drillings in the OE crankshaft is a zero benefit modification and I say this because there is nothing a plug can do that will change my two points above. Moreover, the cetripetal forces are identical at the entry point and for all practical purposes similar at the exit point... plugging one end of the cross-drill cannot result in the same dP as a straight-shot drilling. I'd like to hear any and all opinions...
|