Every now-and-then this subject comes up and the consensus is that the cam timing does change when the cylinder block or head's deck surfaces are milled, but no quantitative numbers have ever been given. This change occurs because the timing belt is a set length (one must assume stretch is negligible), and milling the heads moves the center lines of the camshafts relative to the center lines of the idlers and crankshaft which cause a rotation at the cams with the resulting slack taken up at the timing belt tensioner idler. To set this up, I need to define a few constants: 1) all rotational directions defined are to be while looking at the front of the engine. 2) the crankshaft rotates clockwise (CW). 3) to advance the cam timing, the camshafts must rotate CW while the crankshaft remains stationary. 4) to retard the cam timing, the camshafts must rotate counter-clockwise (CCW) while the crankshaft remains stationary. 5) a cam sprocket OD measures 4.950" 6) all idler OD measure 2.370" 7) due to a combined 100° angle between the intake port surfaces, the lower plenum and its idler will move down 0.0087" for every 0.010" milled off the heads or block. This figure assumes that no material is machined off of the lower plenum to compensate for port alignment (more on this at the end). Below is a CAD drawing of the stock belt layout. I estimate the center to center dimensions are accurate to ±0.050", but this shouldn't be an issue since we are looking at what happens when something changes by a known amount (milling the heads 0.010"). The angles on each sprocket and idler are listed to allow calculating the total belt length engaged on each. The red lines indicate distances that are fixed and will not change.
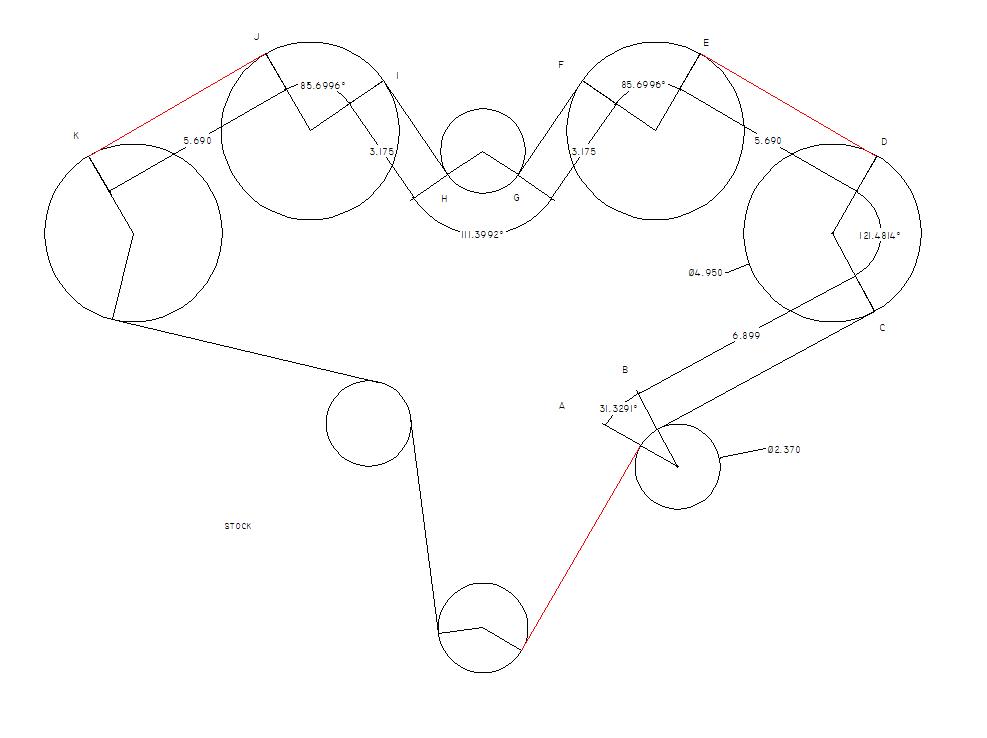 Below is the drawing with the heads milled 0.010" and the lower plenum is NOT machined so the idler is accordingly moved down 0.0087" also.
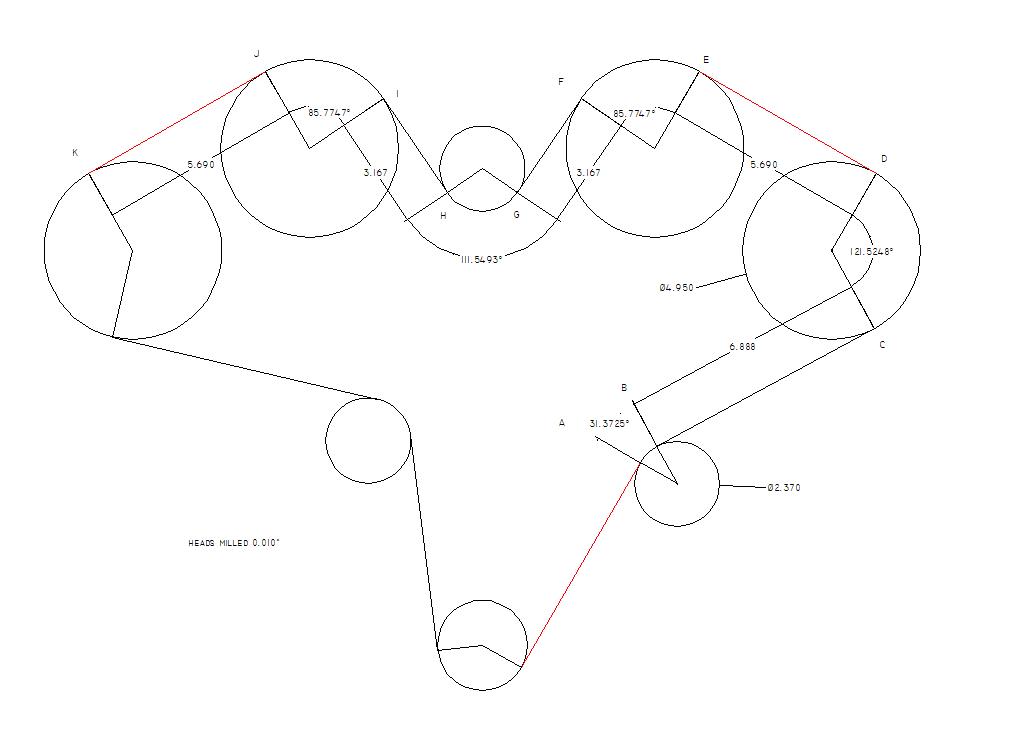 Lastly, here is a drawing which depicts the lower plenum being machined for port alignment (0.0054" from each port surface) which drops the idler a total of 0.0115" from stock.
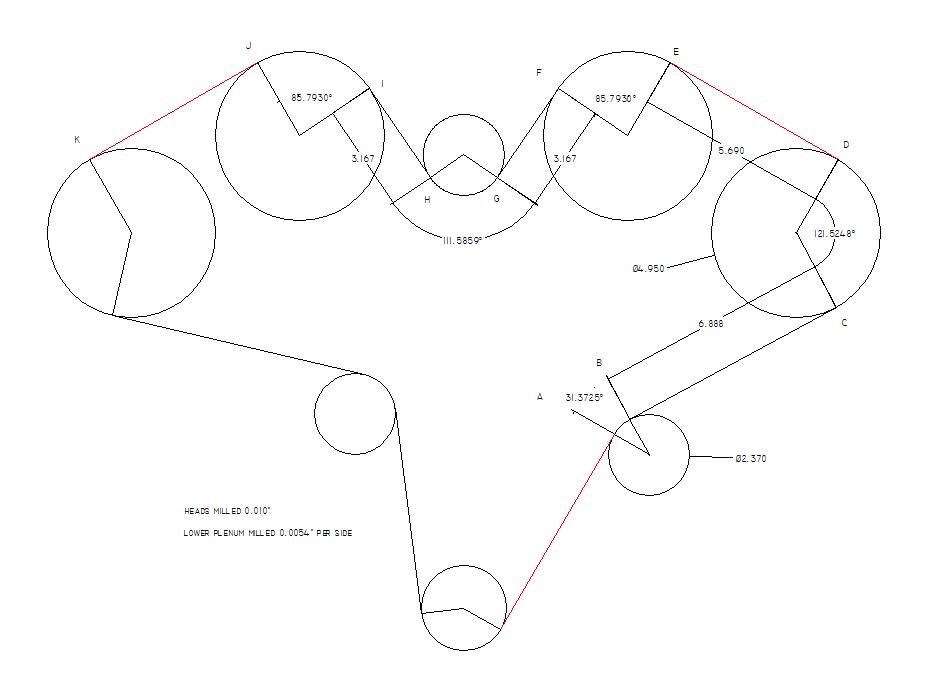 And finally, here is a spreadsheet used to calculate the linear distance for every section A through K and then calculate the timing change for each camshaft. Please note the lower section is an analysis of if you were to mill the lower plenum for port alignment. You can also download the spreadsheet here if you'd like to check the formulas. 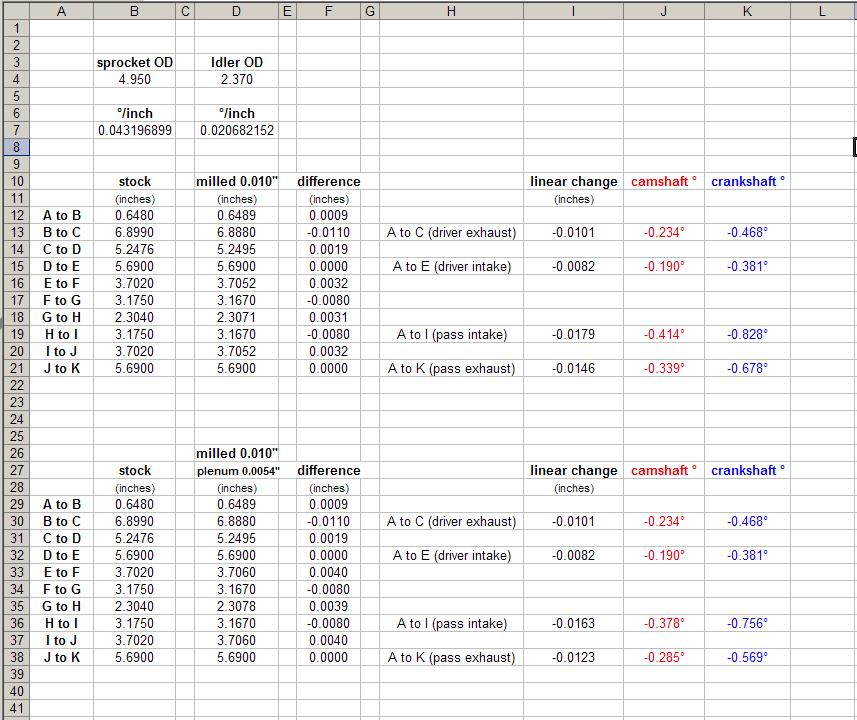
Milling the heads 0.010" retards the camshaft timing for all cams, but it doesn't do it consistently. The passenger intake retards the most at -0.414° (-0.828° crank), while the driver intake retards the least at -0.190° (-0.380° crank)... wow! If you were to mill the lower plenum for port alignment, you would need to remove 0.0054" from each side for every 0.010" removed from the heads. Doing this drops the lower plenum and its idler another 0.0018" (0.0115" total) and affects only the timing for the passenger side camshafts. The overall timing change is a bit less drastic, the passenger intake would be -0.378° (-.0756° crank) and the passenger exhaust would be -0.285° (-0.569° crank). Conversely, if your were to raise the lower plenum with thicker gaskets (there are some available) and no material removal from the port surfaces, this would retard the passenger camshafts even further. So, does all of this mean that if you milled your heads you should run out to buy adjustable sprockets? I really don't know for certain, but I highly doubt a change in cam timing of less than 1° (crank) could be accurately and consistently measured on a dyno.
|