I spent a lot of time reading stuff on the web about hp vs. torque.
I think I have it all figured out now. Although I could be entirely wrong.
:-)
Here's my current dynochart for my mods:
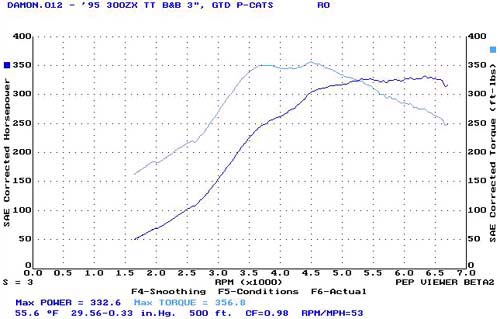
Here's the short & sweet. If I wanted to do what *feels* best, Like
getting a passenger in the car you want to snap the neck of:
1st-2nd: 5823rpm
2nd-3rd: 5196rpm
3rd-4th: 4550rpm
4th-5th: 4666rpm
For *real* acceleration, this is what I have:
1st-2nd: 7200rpm (JWT ECU, let's go to redline)
2nd-3rd: 6850rpm
3rd-4th: 6625rpm
4th-5th: 6625rpm
How did I get these numbers? Let's do the *feel* first, it's easy:
1. Get a dynochart w/ torque & hp vs. RPM
2. Know the gear ratios, these are the same for NA & TT 5spd:
-
1st: 3.21:1
-
2nd: 1.93:1
-
3rd: 1.30:1
-
4th: 1.00:1
-
5th: 0.75:1
3. Find the torque peak value, most dynocharts supply this number.
Mine is 356.8 in this chart. BUT I want to maximize pull in each gear,
so I'll want to start each gear around 3500rpm. That's the front of my
torque 'peak' which stays pretty flat across to 4800rpm. Now we want to
work out the gear ratios to put us at 3500rpm after each shift.
4. Run out the math
3500 = shiftingRPM (gear2/gear1)
For 1-2 gear shift:
3500 = shiftingRPM (1.93/3.21)
3500 = shiftingRPM(.601)
3500/.601 = shiftingRPM
5823 = shiftingRPM
Got it? If I shift at these points, I will land back at 3500rpm &
the front of a 1300rpm peak area to get the snappin' happenin' :-) Peak
torque will equal maximum acceleration for that gear, so I'm trying to
maintain the highest amount of torque across a rev range.
Now, at the track, we're shooting for tangible numbers, measured by
machine. Seat of the pants is out the window. Here's how to do the *real*:
1. Get a dynochart w/ torque & hp vs. RPM
2. Know the gear ratios, these are the same for NA & TT 5spd:
-
1st: 3.21:1
-
2nd: 1.93:1
-
3rd: 1.30:1
-
4th: 1.00:1
-
5th: 0.75:1
3. Gearing is a multiplier for torque, so even if the torque isn't
as high chart wise towards the end, the gearing makes the mechanical difference
& results in maximum acceleration. I'm just going to run down my chart
so you can see how the process works, oh, here's the dyno chart again:
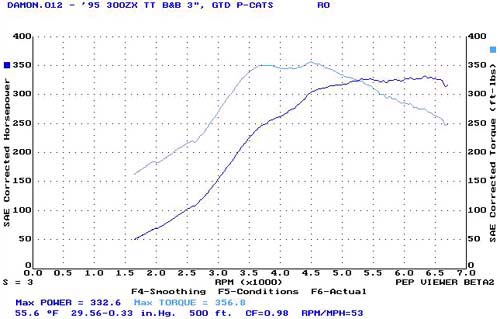
Here's how it works out in a chart:
gear rpm tq output rpm tq output difference
3.21 0000(000)000.00 7200(220)706.20 34.57
1.93 4327(348)671.64 6850(237)457.41 01.11
1.30 4613(351)456.30 6625(255)331.50 00.50
1.00 5096(331)331.00 6650(250)250.00 00.50
0.75 4987(334)250.50 7200(220)165.00 00.00
4. 3.21 0000(000)000.00 is nothing, literally, but the next
chunk is the first shift point: 3.21 7200(220)706.20 -> 1.93 4327(348)671.64
at 7200rpm, the chart shows 220ft-lbs of torque. OK, I know, it really
doesn't... think interpolation for a sec. :-) I'm going to multiply the
torque value by the gear ratio:
220 ft-lbs * 3.21 gear ratio = 706.2 ft-lbs of output shaft torque
5. Now we use the gear ratio finder from above to determine where this
shift point will land us in the next gear:
nextRPM = shiftRPM (gear2/gear1)
nextRPM = 7200(1.93/1.30)
nextRPM = 7200(.601)
nextRPM = 4327RPM
6. At 4327 RPM we see the torque is 348ft-lbs. Multiply this by the
gearing:
348 ft-lbs * 1.93 gear ratio = 671.64 ft-lbs of output shaft torque
This is significantly less (34.57ft-lbs) than the amount of power we
shifted from. Why shift when the ground is still feeling more force then
in the next gear? But, we ran out of RPM to work with, forcing a shift
into the next gear.
For the next gears there's a lot of trial & error. I wrote a script
to do most of the math for me, but it can be done on paper with a little
more time. :-) The easy way is to start graphing the torque from redline
back in 50 RPM measurements. These numbers can be used through all gear
readings, just use different multipliers for gearing. Keep doing the math
until you find a shift point where the output shaft torque is the same
or slightly less in the next gear or as close as possible. The first shift
had a 34.57ft-lbs difference, the rest you can hit very close in the next
gear. The shape of the torque curve will determine how close you can get.
If you want me to polish up the script & make it user friendly I
can...
Uh, then again, I never found anything definitive on how to do this.
I could be way out in left field. Cuss me if necessary. :-)
Dallas DamonZ